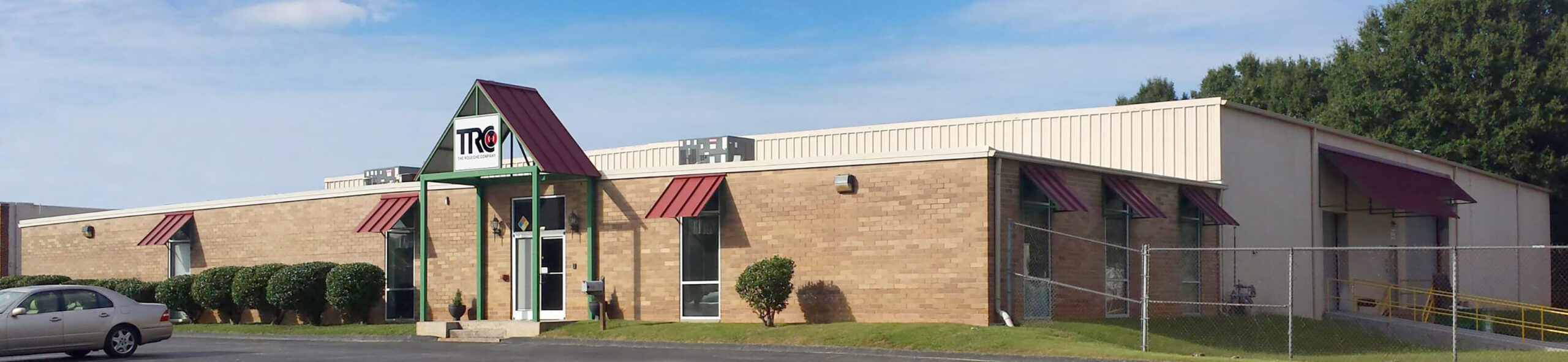
About TRC Welding Systems
THE ROUECHE COMPANY, LLC was established in March, 1999, and began as a Service/Consulting firm for Resistance Spot Welding, and maintaining a single office in downtown Chattanooga, TN.
After just over a year in business, it became apparent that there was a void in the Resistance Welder Machine Building Industry in this area as customers inquired of us to offer them an option to some of the more established companies with whom they had been used to dealing. The machine building process at TRC was born and we are now celebrating our 25th year of operations.
Our design team is skilled, with nearly a century of combined Engineering/Build experience over numerous automotive and industrial applications. This experience allows us to compete globally, with TRC now having welding equipment and automation placed into production both Nationally and Internationally.
All of the equipment manufactured by THE ROUECHE COMPANY is backed with complete training, commissioning and support of our staff.




TRC is an Original Equipment Manufacturer (OEM).
We Design, Machine, Fabricate, Assemble, Program, Test,
and Ship … All from Chattanooga, TN USA.
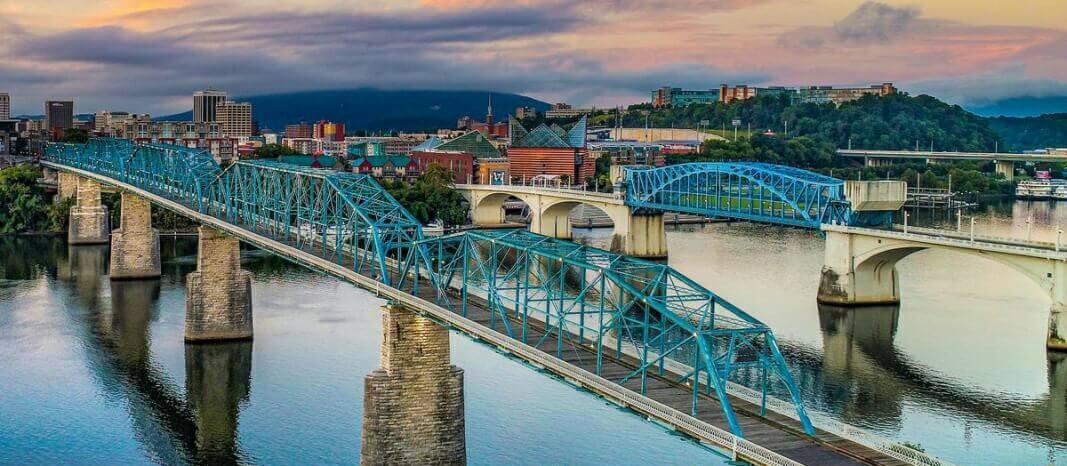