Formal Resistance Welding Seminars and Training
Automatic Robotic and Custom Resistance Welder Systems Classroom Training and Certification!
TRC provides formal training for your staff by way of Customized Resistance Welding Seminars.
This training is designed around your products and staff and is customized to meet your specific needs.
For your convenience, training sessions may be held at your facility, at our TRC facility or virtually.
Classroom and Hands On Education and Instruction in all of these areas of welding discipline!
• Resistance Welding – Defined
• Types of Welding Machines
• Resistance Welders and Components
• Factors In Resistance Welding
• Analysis of “The Process”
• Process Variables
• Ideal Maintenance Practices
• Resistance Welding - Defined
Resistance welding is a widely used metal joining process that involves the application of heat generated by the resistance to electric current flowing through the work pieces. In simpler terms, it’s a technique where two metal pieces are fused together by passing an electric current through them, creating enough heat to melt and join the materials.
Understanding the different types of welding machines allows welders to choose the right tool for the job, considering factors such as material thickness, welding technique, and environmental conditions. Each type offers unique advantages, making welding machines versatile tools in various industries.
• Types of Welding Machines
Welding machines are essential tools in metal fabrication and construction, providing the means to join metals efficiently. There are various types of welding machines, each designed for specific applications and welding techniques. Here’s a brief overview of some common types:
1. Stick Welders (SMAW – Shielded Metal Arc Welding):
– Simple and versatile machines.
– Use a consumable electrode coated in flux.
– Ideal for outdoor use and works well on thick metals.
2. MIG Welders (GMAW – Gas Metal Arc Welding):
– Utilize a wire electrode and a shielding gas.
– Offer high efficiency and produce clean welds.
– Suitable for a range of materials and thickness.
3. TIG Welders (GTAW – Gas Tungsten Arc Welding):
– Provide precise control over the welding process.
– Use a non-consumable tungsten electrode and a shielding gas.
– Ideal for welding thin materials and producing high-quality welds.
4. Flux-Cored Arc Welders (FCAW):
– Similar to MIG welding but use a tubular wire filled with flux.
– Suitable for outdoor welding and works well on dirty or rusty surfaces.
5. Submerged Arc Welders (SAW):
– Employ a granular flux to cover the welding area.
– Ideal for heavy-duty and high-speed welding of thick materials.
6. Spot Welders:
– Designed for spot welding, where metal sheets are joined at specific points.
– Commonly used in automotive manufacturing and sheet metal fabrication.
7. Plasma Arc Welders:
– Use a plasma torch to create a high-velocity jet of ionized gas.
– Suitable for cutting and welding non-ferrous metals.
8. Resistance Welders:
– Utilize electrical resistance to generate heat for welding.
– Include spot welding, seam welding, and projection welding.
9. Automatic Welders:
– Automatic welding machines are designed for semi-automated or fully automated welding processes.
– These machines often use pre-programmed settings for welding parameters and can be programmed to follow specific weld paths.
– Automatic welders are commonly used in high-production environments, improving efficiency and consistency.
10. Robotic Welders:
– Robotic welding systems involve the use of robotic arms equipped with welding tools.
– These systems offer high precision, repeatability, and the ability to handle complex welding tasks.
– Robotic welders are programmable and can be integrated into manufacturing lines for continuous and precise welding operations.
– They enhance productivity and are particularly effective in applications where accuracy and speed are crucial.
Both automatic and robotic welders represent advancements in welding technology, bringing a higher level of automation and precision to the welding process. While automatic welders streamline operations with pre-set parameters, robotic welders take it a step further by introducing robotic arms capable of intricate and repetitive welding tasks. These technologies play a significant role in modern manufacturing, contributing to increased efficiency and the production of high-quality welds.
• Resistance Welders and Components
Resistance welders are specialized machines used for joining metals through the application of heat generated by electrical resistance. The process involves passing an electric current through the work pieces, creating heat at the contact points and causing the materials to melt and fuse together.
Understanding how these components work together is key to achieving successful resistance welding. Proper maintenance and adjustment of these elements contribute to consistent and high-quality welds. Whether it’s spot welding, seam welding, or projection welding, the components of resistance welders play a crucial role in ensuring effective and reliable metal joining processes.
Here’s a brief overview of the key components:
1. Electrodes:
– Electrodes are crucial components that make direct contact with the work pieces.
– They conduct the electric current and apply pressure to ensure proper contact between the metals.
– Electrode materials vary based on the application, and they play a significant role in the quality of the weld.
2. Power Supply:
– The power supply is responsible for providing the electric current required for resistance welding.
– It delivers a controlled and precise amount of electrical energy to generate the necessary heat for welding.
– Different types of resistance welding may require specific power supply configurations.
3. Controller:
– The controller regulates the welding parameters, including current, voltage, and duration.
– It allows for precise adjustments to match the requirements of different materials and thickness.
– Advanced controllers contribute to the consistency and quality of the welds.
4. Transformer:
– In resistance welding, a transformer is used to adjust the voltage levels.
– It helps in stepping down the high voltage from the power supply to the required welding voltage.
– Transformers are integral to maintaining control over the welding process.
5. Cooling System:
– Resistance welding generates significant heat, and a cooling system is essential to prevent overheating.
– Water or air cooling systems are commonly employed to maintain the optimal operating temperature of the machine.
• Factors In Resistance Welding
Resistance welding is a precise and effective method for joining metals, and several factors influence the success of the process.
Understanding and carefully adjusting these factors are key to successful resistance welding. Whether it’s spot welding, seam welding, or projection welding, fine-tuning these parameters ensures consistent results and high-quality welded joints in various industrial applications.
Here’s a brief overview of the key factors in resistance welding:
1. Material Selection:
– The type of metals being welded is a critical factor. Different materials have varying electrical resistance, affecting the heat generated during welding.
2. Electrode Material and Design:
– The choice of electrode material is important, as it directly affects the heat transfer and durability of the weld.
– Proper electrode design ensures even pressure distribution and good contact with the work pieces.
3. Welding Current and Voltage:
– Adjusting the welding current and voltage is crucial for achieving the right level of heat required for welding.
– These parameters depend on the material thickness, type, and the specific requirements of the welding process.
4. Welding Time:
– The duration of the welding process, known as welding time, influences the depth of penetration and the overall quality of the weld.
– Controlling the welding time is essential for achieving consistent and reliable welds.
5. Pressure Applied:
– Proper pressure ensures good contact between the work pieces and electrodes.
– Adequate pressure is necessary for overcoming surface contaminants and achieving a strong bond.
6. Electrode Force Control:
– Monitoring and controlling the force applied by the electrodes contribute to uniform welds.
– Maintaining consistent electrode force is crucial for preventing inconsistencies in the welding process.
7. Cooling Systems:
– Efficient cooling systems prevent overheating of the equipment and ensure continuous, reliable operation.
– Cooling methods, such as water or air cooling, help maintain the optimal temperature during welding.
8. Alignment and Fixture:
– Proper alignment and fixture of the work pieces are essential for achieving accurate and repeatable welds.
– Precise alignment contributes to the overall strength and quality of the welded joints.
• Analysis of “The Process”
“The Process” in resistance welding refers to the step-by-step methodology and intricacies involved in achieving successful and high-quality welds. Analyzing “The Process” is crucial for understanding the factors that contribute to effective resistance welding outcomes. Here’s a brief exploration of the key elements in the analysis of “The Process” for resistance welding:
1. Material Selection:
– The analysis begins with the careful consideration of the materials to be welded. Different metals have varying electrical resistance, affecting the heat generated during the welding process.
2. Electrode Configuration:
– Understanding the electrode configuration is essential. Electrodes play a vital role in transmitting the electric current and applying pressure for proper contact between the work pieces.
3. Optimal Welding Parameters:
– Analyzing and setting the right welding parameters, such as current, voltage, and duration, is critical. These parameters vary based on the material thickness, type, and the specific requirements of the welding process.
4. Electrode Force and Pressure:
– Ensuring the proper electrode force is applied is crucial for achieving good contact and uniform pressure. Analyzing and adjusting the force contributes to consistent and reliable welds.
5. Cooling Systems:
– The analysis extends to the cooling systems in place. Effective cooling systems, whether water or air-based, prevent overheating of the equipment, ensuring continuous and reliable operation.
6. Monitoring and Control:
– Implementing monitoring and control systems contributes to the analysis of “The Process.” Real-time feedback on parameters like temperature and pressure allows for immediate adjustments, ensuring the welding conditions remain within the desired range.
7. Quality Checks and Inspection:
– Incorporating thorough quality checks and inspections into “The Process” is essential. Visual inspections, dimensional checks, and, if needed, non-destructive testing methods contribute to assessing the quality of the weld.
8. Documentation and Record-Keeping:
– Proper documentation of the welding parameters, inspection results, and any adjustments made during the process is part of the analysis. Comprehensive records aid in tracking equipment history and ensuring accountability.
9. Continuous Improvement:
– “The Process” analysis is not static; it involves a commitment to continuous improvement. Regularly reviewing and refining the welding process based on feedback and performance data contributes to ongoing efficiency and quality enhancements.
By delving into the intricacies of each step in “The Process” for resistance welding, manufacturers and welders can optimize their operations. This analytical approach ensures that the welding process is not only effective but also capable of meeting the stringent quality standards required in various industries. The analysis of “The Process” serves as a pathway to achieving consistent, high-quality welds.
• Process Variables
In resistance welding, the achievement of high-quality welds relies on carefully managing and controlling various process variables. These variables play a crucial role in determining the strength, durability, and consistency of the welded joints. Here’s a brief exploration of the key process variables in resistance welding:
1. Current (Amperage):
– The amount of electric current flowing through the work pieces is a fundamental process variable.
– Adjusting the current controls the heat generated during welding, influencing the depth of penetration and overall weld quality.
2. Voltage:
– Voltage is another critical variable that impacts the resistance welding process.
– Proper voltage settings are essential for achieving the right balance of heat generation and preventing issues such as overheating or insufficient fusion.
3. Time (Welding Cycle):
– The duration of the welding cycle, commonly referred to as welding time, is a key variable.
– Controlling the time the current flows through the workpieces influences the size and strength of the weld.
4. Pressure (Force):
– Electrode force, or the pressure applied to the work pieces, is crucial for ensuring good contact and uniform pressure during welding.
– Adequate pressure contributes to overcoming surface contaminants and creating a strong bond.
5. Electrode Material and Design:
– The type of material used for electrodes and their design significantly impact the welding process.
– Proper electrode selection ensures efficient heat transfer, even pressure distribution, and overall welding success.
6. Electrode Geometry:
– The shape and configuration of the electrode tips influence the distribution of heat during welding.
– Optimal electrode geometry helps achieve uniform heating and avoids issues like overheating or inadequate fusion.
7. Cooling Systems:
– Effective cooling systems help maintain the optimal operating temperature of the equipment.
– Controlling the cooling process is vital for preventing overheating and ensuring continuous, reliable operation.
8. Material Properties:
– The properties of the materials being welded, such as conductivity and thickness, are inherent process variables.
– Different materials require adjustments in other variables to achieve optimal welding results.
9. Alignment and Fixtures:
– Proper alignment of the work pieces and fixture is crucial for achieving accurate and repeatable welds.
– Misalignment can lead to inconsistencies in the welding process.
Understanding and carefully adjusting these process variables are key to achieving successful resistance welding. Fine-tuning the current, voltage, time, pressure, and other parameters ensures consistent results and high-quality welded joints in various industrial applications. Manufacturers and welders who master the control of these variables can optimize their resistance welding processes for efficiency and reliability.
• Ideal Maintenance Practices
Ideal maintenance practices play a pivotal role in ensuring the longevity, efficiency, and safety of equipment and machinery across various industries. Whether it’s a manufacturing plant, construction site, or any other operational setting, adopting sound maintenance practices is essential for preventing breakdowns, optimizing performance, and minimizing downtime.
By incorporating these ideal maintenance practices into operational routines, organizations can enhance the reliability of their equipment, improve safety conditions, and optimize overall efficiency. Proactive maintenance not only prevents unplanned downtime but also contributes to cost savings and the longevity of valuable assets.
Here’s a brief overview of ideal maintenance practices:
1. Regular Inspection and Lubrication:
– Conduct routine inspections to identify wear and tear, loose parts, or potential issues before they escalate.
– Regularly lubricate moving parts to reduce friction, prevent corrosion, and extend the life span of components.
2. Scheduled Preventive Maintenance:
– Establish a proactive preventive maintenance schedule based on equipment manufacturer recommendations and industry standards.
– Regularly replace worn-out parts, check fluid levels, and perform necessary adjustments to prevent unexpected failures.
3. Cleaning and Housekeeping:
– Maintain a clean and organized workspace to prevent the accumulation of debris, dust, or contaminants.
– A clean environment contributes to equipment reliability and enhances overall safety.
4. Training and Skill Development:
– Provide training to maintenance personnel to ensure they are equipped with the skills and knowledge needed for effective troubleshooting and repairs.
– Stay updated on new technologies and advancements relevant to the equipment being maintained.
5. Record Keeping and Documentation:
– Keep detailed records of maintenance activities, including dates, performed tasks, and any issues discovered.
– Documentation aids in tracking equipment history, planning future maintenance, and ensuring compliance with regulatory requirements.
6. Predictive Maintenance Techniques:
– Implement predictive maintenance techniques such as vibration analysis, thermograph, or oil analysis.
– These techniques help identify potential issues before they lead to equipment failure, allowing for timely intervention.
7. Equipment Calibration:
– Regularly calibrate measurement and control devices to ensure accurate readings.
– Proper calibration contributes to the precision and reliability of equipment performance.
8. Emergency Preparedness:
– Develop and regularly update emergency maintenance procedures to handle unexpected breakdowns or critical failures.
– Having a well-defined plan in place helps minimize downtime and facilitates swift response in case of emergencies.
9. Collaboration and Communication:
– Foster collaboration and communication between maintenance teams and other departments.
– Ensure that relevant information about equipment conditions, maintenance schedules, and issues is shared promptly.
• Training and Instruction
• Lab Instruction
• Hands-on Instruction
• Weld / Process Monitoring
• Set-up Procedures for Spot Welders
• Useful Welding Charts
• Evaluating the Quality of the Weld
• Training and Instruction
TRC Welding is dedicated to providing comprehensive training in resistance welding through a combination of laboratory (lab) instruction and hands-on experiences. This approach ensures that participants not only gain theoretical knowledge but also develop practical skills essential for success in the field of resistance welding.
Combining lab and hands-on instruction creates a well-rounded training experience. Participants not only grasp the theoretical underpinnings of resistance welding but also gain the practical skills necessary for success in the industry. TRC Welding’s commitment to this comprehensive approach ensures that individuals completing the training program are equipped with the knowledge and proficiency needed to excel in the field of resistance welding.
• Lab Instruction
In the lab, participants are introduced to the fundamental principles of resistance welding. Theoretical concepts related to electrical resistance, welding current, and electrode materials are covered in-depth. TRC Welding employs state-of-the-art laboratories equipped with modern tools and equipment, creating an ideal learning environment for students.
Lab instruction allows participants to:
1. Understand Welding Fundamentals:
– Learn the theoretical foundations of resistance welding, including how electric current generates heat and forms strong bonds between metals.
2. Explore Equipment:
– Familiarize themselves with different types of resistance welding machines and understand their functionality.
3. Gain Insight into Welding Processes:
– Explore various resistance welding processes, such as spot welding, seam welding, and projection welding, to understand their applications and advantages.
• Hands-on Instruction
Hands-on instruction is a key component of TRC Welding’s training program. This practical aspect enables participants to apply the knowledge gained in the lab to real-world scenarios. Under the guidance of experienced instructors, participants engage in hands-on activities that simulate actual resistance welding processes.
Hands-on instruction allows participants to:
1. Practice Welding Techniques:
– Develop proficiency in operating resistance welding machines and practicing different welding techniques.
2. Refine Skills:
– Hone their skills in electrode selection, electrode force adjustment, and controlling welding parameters to achieve high-quality welds.
3. Troubleshoot Issues:
– Learn to identify and address common challenges and issues that may arise during resistance welding.
4. Ensure Safety Compliance:
– Emphasize safety practices, ensuring that participants are well-versed in safety protocols when working with welding equipment.
• Weld / Process Monitoring
Weld/process monitoring is a crucial aspect of welding operations, ensuring the quality and consistency of welded joints. This involves the use of monitoring techniques and equipment to assess and control various aspects of the welding process.
Weld/process monitoring plays a vital role in modern manufacturing, ensuring that welding operations meet the required standards and produce reliable, high-quality welds. By leveraging monitoring technologies, manufacturers can enhance the efficiency, accuracy, and consistency of their welding processes across various industries.
Here’s a brief overview of weld/process monitoring:
1. Real-time Monitoring:
– Welding processes are monitored in real-time to detect deviations from set parameters.
– Real-time monitoring allows for immediate adjustments, ensuring that the welding conditions remain within the desired range.
2. Sensors and Instruments:
– Various sensors and instruments are used to measure parameters such as temperature, voltage, current, and pressure during welding.
– These sensors provide data that helps in assessing the quality of the weld and identifying any anomalies.
3. Quality Control:
– Weld/process monitoring is an integral part of quality control in manufacturing.
– By continuously monitoring the welding parameters, manufacturers can ensure that the final product meets the required standards.
4. Defect Detection:
– Monitoring helps in early detection of defects or irregularities in the welding process.
– This proactive approach allows for corrective actions to be taken before defective welds lead to production issues.
5. Data Logging and Analysis:
– Data logging systems record information from the welding process for further analysis.
– Analyzing this data provides insights into the performance of the welding equipment and helps optimize the process for efficiency and quality.
6. Automated Systems:
– Advanced welding systems often incorporate automated monitoring features.
– Automated monitoring systems can adjust welding parameters on the fly, contributing to consistent and high-quality welds.
7. Process Optimization:
– Continuous monitoring allows for the optimization of welding parameters to enhance efficiency and reduce the likelihood of defects.
– Manufacturers can fine-tune the welding process based on real-time data, improving overall productivity.
• Set-up Procedures for Spot Welders
Setting up a spot welder is a crucial step to ensure efficient and effective metal joining. Spot welding is a process where metal sheets are joined at specific points by the application of heat through electrical resistance.
By following these setup procedures, welders can establish the right conditions for spot welding, leading to consistent and reliable results. Proper setup is essential for achieving strong and durable spot welds, making it a fundamental step in the metal joining process.
Here’s a brief guide on the setup procedures for spot welders:
1. Material Preparation:
– Ensure that the metal sheets to be welded are clean and free from any contaminants such as rust, grease, or paint.
– Properly align and secure the work pieces in the desired position for spot welding.
2. Selecting Electrodes:
– Choose the appropriate electrodes based on the material being welded and the specific requirements of the application.
– Electrodes should provide good conductivity, even pressure distribution, and suitable heat transfer.
3. Adjusting Electrode Force:
– Set the electrode force to ensure proper contact between the electrodes and the work pieces.
– Adequate force is necessary to overcome surface contaminants and create a strong bond.
4. Setting Welding Current and Time:
– Adjust the welding current and time settings on the spot welding machine.
– The appropriate settings depend on factors such as material thickness, type, and the desired strength of the weld.
5. Checking Electrode Alignment:
– Verify that the electrodes are aligned correctly to ensure precise and consistent spot welds.
– Misaligned electrodes can result in uneven welds and compromise the overall quality.
6. Testing and Calibration:
– Conduct test spot welds on scrap material to ensure that the machine is functioning correctly.
– Calibrate the spot welder based on the test results and make necessary adjustments to achieve the desired weld quality.
7. Cooling System Check:
– Ensure that the spot welder’s cooling system is functioning properly.
– Spot welding generates heat, and an efficient cooling system helps maintain the optimal operating temperature of the machine.
8. Safety Precautions:
– Prioritize safety by wearing appropriate personal protective equipment, including safety glasses and gloves.
– Follow safety guidelines and precautions outlined in the spot welder’s user manual.
• Useful Welding Charts
Charts play a valuable role in resistance welding, providing a visual reference for key parameters and helping operators make informed decisions during the welding process. These charts are essential tools for achieving consistency and quality in resistance welding applications. Here’s a brief overview of some useful charts for resistance welding:
1. Weld Schedule Charts:
– Weld schedule charts outline the recommended combinations of current, voltage, and time for specific welding applications.
– These charts serve as quick references for setting up resistance welding machines, ensuring optimal parameters for different materials and thickness.
2. Resistance Spot Welding (RSW) Charts:
– RSW charts provide guidelines for spot welding parameters, including electrode force, welding current, and weld time.
– These charts are essential for achieving proper penetration and fusion in spot welding applications.
3. Projection Welding Charts:
– Projection welding charts offer guidance on the parameters required for effective projection welding.
– They specify current, voltage, and time settings based on factors such as material type, thickness, and the design of the projections.
4. Pressure vs. Current Charts:
– These charts illustrate the relationship between electrode pressure and welding current.
– Operators can refer to these charts to find the optimal balance that ensures proper fusion without excessive force.
5. Cooling Curve Charts:
– Cooling curve charts provide insights into the cooling rates of welded joints after the welding process.
– These charts help operators understand the cooling characteristics and make adjustments to prevent issues such as rapid cooling-induced cracking.
6. Material Compatibility Charts:
– Material compatibility charts offer information on the compatibility of different materials for resistance welding.
– They help operators choose suitable combinations to achieve strong and reliable welds.
7. Joint Design Charts:
– Joint design charts provide guidelines for the proper configuration of weld joints.
– These charts help in designing weld joints that facilitate optimal heat distribution and fusion during the welding process.
8. Electrode Force vs. Material Thickness Charts:
– These charts assist in determining the appropriate electrode force based on the thickness of the materials being welded.
– Ensuring the right electrode force is crucial for achieving consistent and reliable welds.
9. Weld Quality Evaluation Charts:
– Charts for weld quality evaluation outline visual and dimensional criteria for assessing the quality of welded joints.
– They serve as reference tools for inspectors and operators to ensure compliance with quality standards.
Utilizing these charts in resistance welding applications enhances the precision and efficiency of the process. They empower operators with valuable information, guiding them to make informed decisions that contribute to consistent, high-quality welds. Manufacturers and welders who incorporate these charts into their practices can optimize their resistance welding processes for optimal results.
• Evaluating the Quality of the Weld
Evaluating the quality of a weld is a crucial step in ensuring the strength and reliability of the joined materials. Whether it’s spot welding, arc welding, or any other welding process, a thorough inspection helps identify potential issues and ensures that the final product meets the required standards.
By systematically evaluating these aspects, welders and inspectors can determine the overall quality of a weld. Identifying and addressing potential issues early in the process contribute to the production of reliable, high-quality welds, meeting the stringent demands of various industries.
Here’s a brief guide on evaluating the quality of a weld:
1. Visual Inspection:
– Begin with a visual inspection of the weld. Look for signs of uniformity, proper fusion, and consistent bead appearance.
– Check for any visible defects such as cracks, porosity, or incomplete penetration.
2. Dimensional Checks:
– Measure the dimensions of the weld to ensure it meets the specified requirements.
– Verify the width, depth, and length of the weld against the design or welding procedure specifications.
3. Weld Bead Profile:
– Examine the weld bead profile for a smooth and even appearance.
– Irregularities in the bead shape or size may indicate issues with the welding parameters.
4. Penetration Assessment:
– Assess the depth of penetration into the base material.
– Incomplete penetration or excessive penetration can compromise the strength of the weld.
5. Surface Contamination:
– Check for any surface contaminants that may have affected the welding process.
– Contaminants such as oil, rust, or paint can lead to poor weld quality.
6. Macroscopic Examination:
– Conduct macroscopic examination, if necessary, to inspect the internal structure of the weld.
– This is particularly relevant for critical applications where a detailed examination of the weld’s internal integrity is required.
7. Non-Destructive Testing (NDT):
– Employ non-destructive testing methods such as ultrasonic testing, X-ray inspection, or magnetic particle testing for a more in-depth assessment.
– NDT techniques can reveal hidden defects without damaging the welded joint.
8. Quality Standards Compliance:
– Ensure that the weld meets industry or project-specific quality standards and codes.
– Compliance with standards is essential for guaranteeing the structural integrity and safety of the welded components.
9. Documentation:
– Maintain detailed documentation of the welding parameters, inspection results, and any corrective actions taken.
– Proper documentation is essential for quality control and accountability.
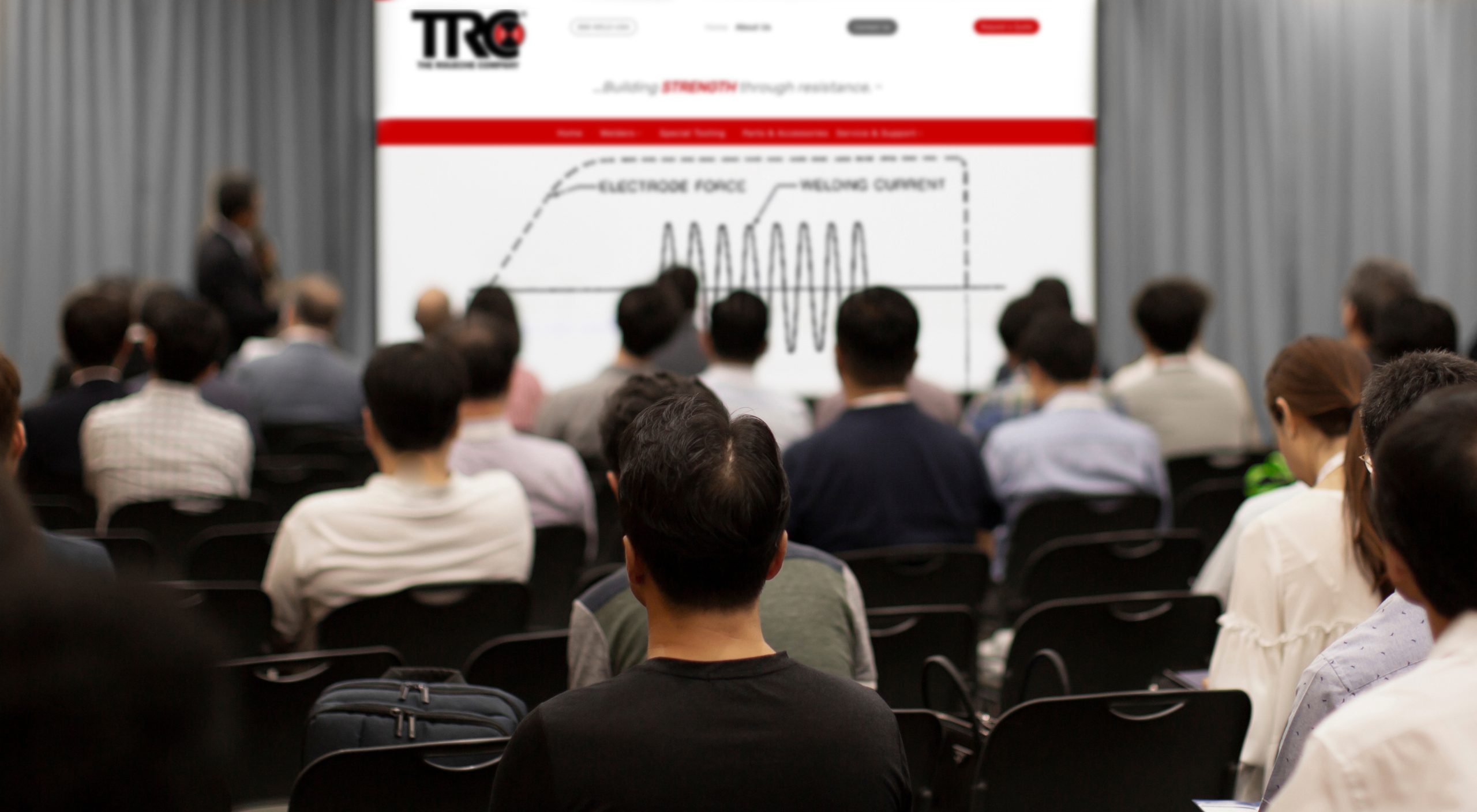